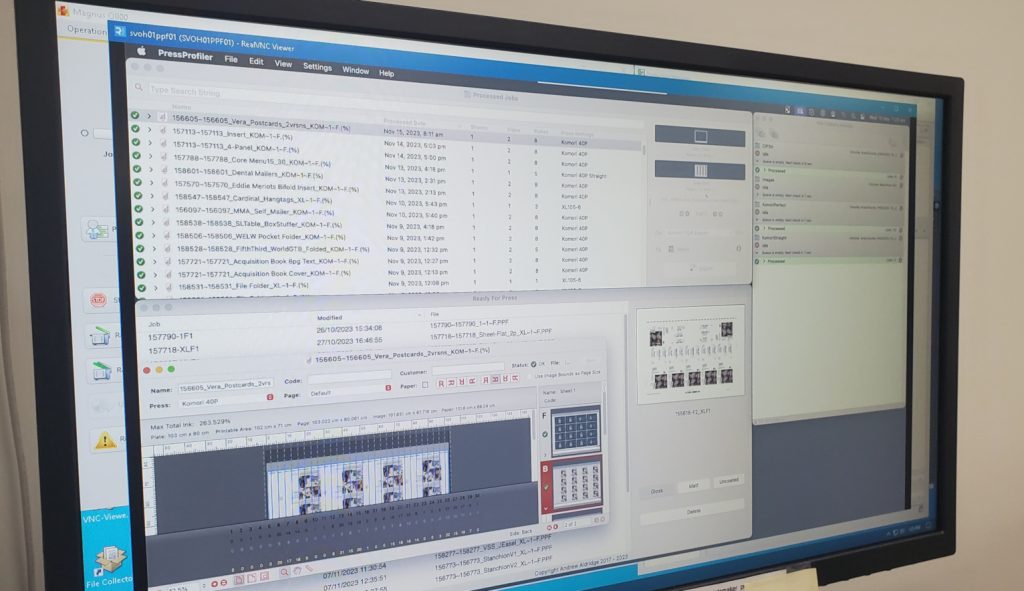
The latest success in the United States for UK-based software supplier Prepress UK has been with Ohio-based Baesman. The installation of Prepress UK’s leading press interface product, PressProfiler CIP3, initially helped the marketing communications group to get the most from its Heidelberg XL105 litho press, and has more recently also enabled the printing team to interface its 8-colour Komori 40P to the same system, simply by purchasing an extra license from Prepress UK.
Baesman Group creates personalized marketing strategies to transform direct-to-consumer campaigns from one-to-many to one-to-one through customer insights, marketing strategy, custom technology solutions, and personalized multichannel execution. Baesman accelerates customer engagement and loyalty by leveraging customer data and delivering personalized messages online, in-store, and through direct mail, email, and SMS. The company includes print production, with both sheet-fed litho and digital printing solutions, among its on-site communications tools.
Prepress UK is an independent supplier of pre-press equipment and software, including specialist software solutions, backed by an unparalleled personal service from initial enquiry through post-sales support.
The PressProfiler CIP3 system helps to automate make-ready on sheet-fed litho presses, saving both time to good copy, as well as paper and consumables, using PressProfiler’s CIP3 ink coverage data, which can provide the link from a pre-press workflow to the presses own system. The software package ensures accurate ink-key pre-setting data for faster press make-ready. This, in turn, helps to ensure fewer run-up sheets are required and a reduced time before correct colour is achieved on the press.
The fact that just one PressProfiler CIP3 software package can be interfaced to two different brands of press – one German and one Japanese – illustrates just how adaptive, and how affordable, this solution is for printers.
Baesman’s Prepress Technical Lead, Dave Harkness, commenting on his initial impressions of PressProfiler, said: “We liked the ease of use of the system. It certainly appeared capable of driving detailed ink data accurately to the press, which was our main aim.
“Once installed the software has been accurate and stable. We did need to have some adjustment made to the package regarding our press naming conventions, but this was handled swiftly by the Prepress UK team. The product offers us the ability to shift from one printing unit to another to meet run sequences on demand on a job-to-job basis.”
Tweaks and adjustments to the software can all be done via the internet, so having a UK-based supplier is not an issue at all. “Support from Prepress UK has been responsive, timely, and on-point with what we needed to receive for full transparency and functionality with our staff,” added Dave Harkness.
One other important reason for using the Prepress UK software: its affordability. “We were able to get the PressProfiler CIP3 package running and tailored to our specific needs for around $10,000 dollars – and all in just a few days. The equivalent package from a press supplier could have cost something north of $40,000 – and that would be for each press! The hugely advantageous thing with using PressProfiler CIP3 is that we’ve been able to use just the one software installation for two presses, from two totally different manufacturers, just by purchasing an extra license,” said Dave Harkness.
Adding further comment, Andrew Dawson, Vice President of Operations, said: “The ease of working with this system allows for it to be very quickly picked up by our press operators, and is just another step forward with our focus on driving efficiencies through our workflows and operations. It has to be said, the cost saving was also a nice bonus.”
PressProfiler is a one-time purchase from Prepress UK – the printer then owns the software for life. It comes with one-year of remote support and then an optional, low-cost, contract is available from year two onwards. In contrast, some press suppliers are now requiring customers who wish to upgrade or connect a new press to purchase their latest CIP3 software with an upfront cost and then on-going monthly subscription.
Nic Chapman, Sales Director at Prepress UK, said: “Remote installation from the UK saves time and money to get the system connected, and also the “air miles”, with the associated pollution that extra flights would produce. Modern presses can connect with PressProfiler CIP3 directly over the network, and will work in the same way as a press suppliers’ original system, but at a fraction of the price.
“That saving is amplified even more when a print business uses machines from more than one manufacturer. One PressProfiler CIP3 package is often all that is needed to interface to different brands of press. Users will just need to purchase an extra license, and not buy the whole package again.”
PressProfiler communicates directly to a wide range of press consoles in their native format, including products from Heidelberg, Koenig & Bauer, manroland sheet-fed, RMGT / Ryobi, Komori, and many others. Integrating with any workflow or RIP, it works with incoming PDF, PS, TIFF or PPF (CIP3) files.
About Baesman Group
Baesman Group creates personalized marketing strategies to transform direct-to-consumer campaigns from one-to-many to one-to-one through customer insights, marketing strategy, custom technology solutions, and personalized multichannel execution. Baesman accelerates customer engagement and loyalty by leveraging customer data and delivering personalized messages online, in-store, and through direct mail, email, and SMS.